Reasons to use a winter front:
Winter fronts on DD engines are necessary due to the design of the engine cooling system. The coolant thermostat is on the inlet side of the cooling system on the DD Platform engine and regulates coolant flow from the radiator into the engine. The thermostat regulates coolant flow to control the temperature of the coolant within the coolant circuit. The following benefits are a result from regulating the coolant at the inlet temperature side of the engine:
- Reduced thermal cycling of the engine
- Operating temperature of the engine is reached faster
- Improved vehicle heating because of the better temperature regulation
Dangers of the using the wrong winter front:
Use of a winter front on a DD platform engine, especially those that are fully closed, it’ll cause performance issues and is not recommended on DD engines. Winter fronts can result in the following:
- Excessive fan run time due to higher CAC outlet temperatures resulting from low air flow through the CAC
- Increase in fuel consumption
- Failure of the DEF system heaters to turn on when needed causing fault codes to appear, poor Aftertreament performance and power loss. Worst case engine shutdown.
- Failure of emission components that will result in a derate and possibly engine shutdown.
Use of a winter front should be avoided as this has been shown to cause false fault codes with the engine and aftertreatment system. This has also been linked to specific component failures that will cause vehicle downtime and lost productivity.
There are two specific situations where a winter front may be temporarily needed:
- To improve cab heating while idling under extreme cold ambient temperature
- When the ambient temperature remains below -30°C and the engine is unable to maintain running coolant temperature of 80°C during normal on road operation.
If either of the above situations is encountered, then a winter front may be temporarily used. A minimum of 25% of the grill must be open in sectioned stripes that run perpendicular to the charge air cooler tube flow direction. This assures even cooling across each tube and reduces header-to-tube stress and possible failure. 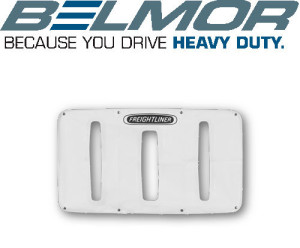